A Comprehensive Guide to the Process and Benefits of Plastic Extrusion
In the huge world of manufacturing, plastic extrusion becomes a crucial and very reliable process. Translating raw plastic into continual profiles, it deals with a variety of markets with its remarkable versatility. This guide aims to elucidate the detailed actions included in this method, the kinds of plastic appropriate for extrusion, and the game-changing benefits it brings to the market. The ensuing conversation guarantees to unfold the real-world effects of this transformative process.
Understanding the Essentials of Plastic Extrusion
While it may appear complicated at initial glance, the procedure of plastic extrusion is fundamentally easy - plastic extrusion. It is a high-volume production strategy in which raw plastic is melted and shaped into a constant profile. The procedure begins with the feeding of plastic product, in the type of pellets, granules, or powders, into a warmed barrel. The plastic is after that melted making use of a combination of warm and shear, applied by a rotating screw. Once the molten plastic reaches completion of the barrel, it is forced with a tiny opening understood as a die, shaping it into a wanted form. The shaped plastic is then cooled down, strengthened, and cut into desired lengths, completing the process.
The Technical Refine of Plastic Extrusion Explained
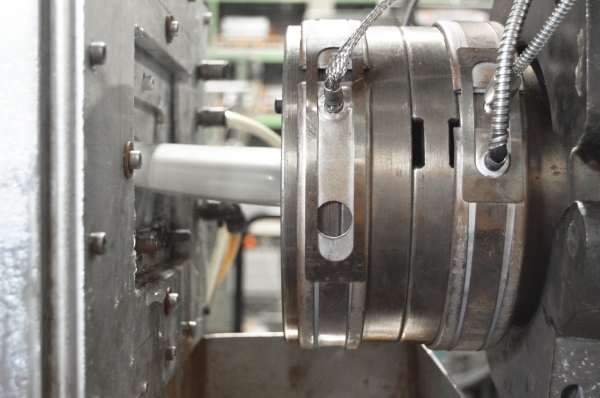
Sorts Of Plastic Suitable for Extrusion
The choice of the right type of plastic is a critical facet of the extrusion procedure. Different plastics supply special buildings, making them much more matched to particular applications. Recognizing these plastic kinds can dramatically enhance the extrusion procedure.
Comparing Plastic Extrusion to Various Other Plastic Forming Techniques
Comprehending the types of plastic ideal for extrusion leads the way for a wider conversation on how plastic extrusion piles up against other plastic developing approaches. Plastic extrusion is unrivaled when it comes to developing continuous accounts, such as pipes, gaskets, and seals. It likewise enables for a constant cross-section along the size of the item.
Key Benefits of Plastic Extrusion in Manufacturing
In the world of manufacturing, plastic extrusion offers several significant advantages. One noteworthy benefit is the cost-effectiveness of the procedure, that makes it a financially enticing production method. Additionally, this strategy gives exceptional product flexibility and enhanced production rate, thus raising general manufacturing performance.
Economical Manufacturing Approach
Plastic extrusion leaps to the center as a cost-efficient manufacturing method in manufacturing. This process stands out for its ability to create high volumes of product swiftly and efficiently, providing producers with considerable savings. The key cost benefit is the ability to use much less costly basic materials. Extrusion makes use of polycarbonate products, which are less expensive compared to steels or porcelains. Additionally, the extrusion process itself is fairly basic, lowering labor costs. In addition, plastic extrusion calls for much less energy than standard manufacturing techniques, adding to lower functional costs. The process also reduces waste, as any kind of excess or malfunctioning products can be recycled and recycled, giving another helpful hints layer of cost-effectiveness. Overall, the monetary advantages make plastic extrusion an extremely eye-catching alternative in the manufacturing market.

Superior Product Adaptability
Beyond the cost-effectiveness of plastic extrusion, another significant benefit in manufacturing lies in its premium item versatility. This makes plastic extrusion an ideal option for industries that require customized plastic elements, such as auto, building and construction, and packaging. In significance, plastic extrusion's product adaptability fosters technology while enhancing functional effectiveness.
Improved Production Rate
A considerable benefit of plastic extrusion exists in its enhanced production rate. Few other production processes can match the rate of plastic extrusion. In addition, the ability to preserve constant article source high-speed production without giving up product high quality sets plastic extrusion apart from various other techniques.
Real-world Applications and Impacts of Plastic Extrusion
In the world of manufacturing, the method of plastic extrusion holds profound importance. This process is widely utilized in the manufacturing of a selection of items, such as plastic tubes, home window structures, and weather stripping. Therefore, it substantially influences markets like building and construction, product packaging, and automobile industries. Its effect prolongs to day-to-day things, from plastic bags to toothbrushes and disposable cutlery. The financial benefit of plastic extrusion, primarily its high-volume and affordable outcome, has reinvented production. Nevertheless, the environmental impact of plastic waste continues to be a concern. For that reason, the sector is constantly making every effort for innovations in biodegradable and recyclable materials, showing a future where the advantages of plastic extrusion can be retained without jeopardizing environmental sustainability.
Verdict
To conclude, plastic extrusion is a reliable and very reliable technique of transforming resources right into varied products. It offers numerous benefits over other plastic forming methods, consisting of cost-effectiveness, high outcome, very little waste, and layout versatility. Its impact is greatly felt in various industries such as building, auto, and durable goods, making it an essential process in today's manufacturing landscape.
Diving deeper into the technological process of plastic extrusion, it starts with the choice of the suitable plastic material. As soon as cooled, the plastic is reduced right into the required sizes or injury onto reels if the product is this link a plastic film or sheet - plastic extrusion. Comparing Plastic Extrusion to Various Other Plastic Forming Techniques
Comprehending the kinds of plastic appropriate for extrusion leads the method for a broader conversation on how plastic extrusion piles up against various other plastic forming techniques. Few various other manufacturing procedures can match the speed of plastic extrusion.