Discovering the World of Steel Stamping: From Layout to Manufacturing
Within the realm of manufacturing, steel stamping attracts attention as an accurate and efficient method for shaping metal sheets into numerous types with remarkable consistency. From the initial design stage where intricate patterns form to the complex production procedures, metal marking is a blend of artistry and design. Exploring this globe unveils an intricate interplay of creativity and technological proficiency, using a glance right into a realm where development fulfills workmanship.
History of Metal Stamping
Steel stamping, an extensively made use of manufacturing procedure today, has a rich background that goes back to old times (Metal Stamping). The beginnings of steel stamping can be mapped to old human beings such as the Egyptians, that utilized stamping strategies to embellish precious jewelry and ornaments with complex designs. Gradually, steel marking advanced, with worlds like the Greeks and Romans utilizing it for producing coins and attractive things
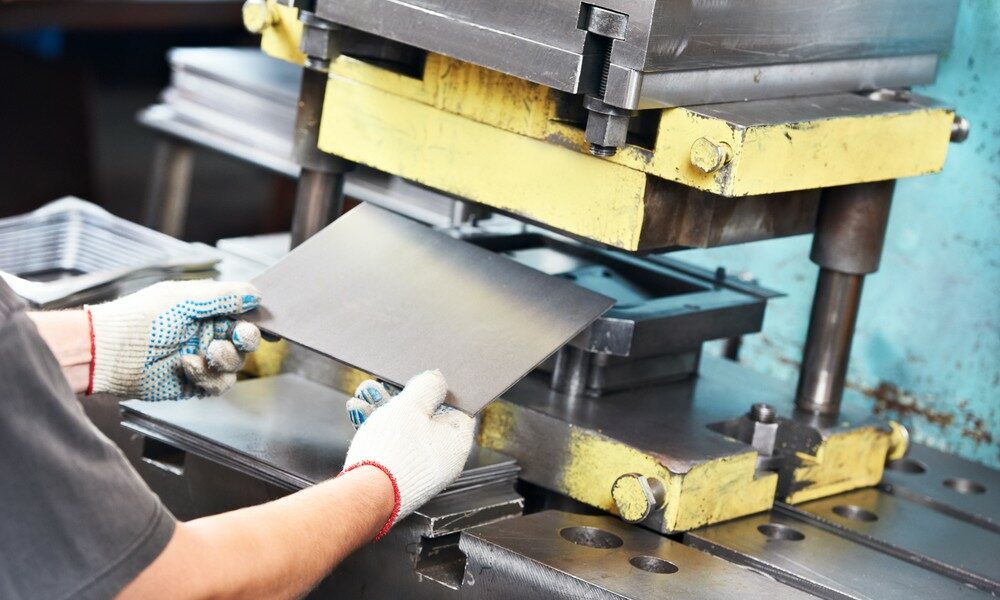
In the 20th century, steel marking remained to progress with the combination of automation and computer mathematical control (CNC) modern technology. These innovations better increased the efficiency and precision of steel marking procedures, making it an essential component of modern production throughout industries such as automobile, aerospace, and electronic devices. Today, steel marking continues to be a vital manufacturing process, integrating tradition with innovation to fulfill the needs of a frequently developing industry.
Layout Factors To Consider and Prototyping
Design factors to consider in metal stamping consist of product choice, part geometry, tooling layout, and manufacturing expediency. Tooling style plays a considerable duty in the success of metal stamping projects, impacting component accuracy, tool durability, and manufacturing performance.
Prototyping is a critical phase in the metal stamping procedure that enables designers to examine the layout, validate manufacturability, and make required modifications prior to you can try this out full-scale production. Prototyping helps recognize possible problems beforehand, conserving time and costs in the future. It additionally provides an opportunity to optimize the layout for performance and high quality. By thoroughly taking into consideration design elements and making use of prototyping, suppliers can improve the metal marking process and achieve high-quality, cost-efficient production results.
Tooling and Equipment Basics
Taking into consideration the essential function that tooling style plays in the success of metal stamping jobs, comprehending the essential devices and tools required is critical for attaining reliable manufacturing end results. Tooling is a basic facet of steel marking, as it straight affects the high quality and uniformity of their explanation the end products. Important tools consist of dies, punches, and fixtures, which are custom-made to shape and form the steel into the preferred parts. Dies are the primary device used to cut and form the steel, while punches help produce holes or certain shapes. Fixtures hold the metal in location during the marking procedure, guaranteeing precision and repeatability. In addition, devices such as marking presses, feeders, and coil handling systems are vital for automating the stamping process and increasing productivity. Purchasing high-grade tooling and devices not only enhances manufacturing performance however also causes greater precision, decreased waste, and overall expense financial savings in steel marking procedures.
Manufacturing Refine and High Quality Control
Efficiently handling the production process and implementing durable top quality look what i found control procedures are important for ensuring the success of steel marking jobs. The production process in metal stamping involves a series of actions that need to be meticulously worked with to accomplish ideal results.
Quality control in metal marking is extremely important to provide items that fulfill the needed requirements. By preserving stringent top quality control standards, producers can maintain their reputation for delivering top quality steel marked products.
Applications and Market Insights
In the world of metal marking, the successful application of production procedures and high quality control procedures directly affects the efficiency and integrity of numerous industry applications and gives beneficial insights into the sector's functional dynamics. Additionally, metal marking helps with the manufacturing of numerous household appliances, including fridges, washing equipments, and ovens, by providing affordable remedies for manufacturing resilient and complex components. Recognizing the applications and sector understandings of metal stamping is crucial for maximizing manufacturing procedures and improving item top quality throughout different markets.

Verdict
Finally, metal marking has an abundant background and plays a critical duty in numerous industries. Design considerations, prototyping, tooling, devices, manufacturing procedures, and quality assurance are important aspects of metal stamping. With its prevalent applications and sector insights, steel marking remains to be a flexible and efficient manufacturing process. By recognizing and making use of the concepts of steel marking, producers can achieve high-quality, accuracy parts for a range of items.